Plastic Injection Molding
Key Benefits:
- Wear resistance, especially glass filled resins
- Release, lubricity
- Flow rate, lubricity
- Improved cycle times, lubricity
- Thin, even deposit for conformance to geometry without re-machining
- Can be re-applied many times over, minimizing cost of new molds
- Chemical attack resistance, gassing
- Low temp process will not affect part geometries
- Uniform cooling, improved cycle times
- Thermal conductivity, mirrors substrate, no hot/cold spots due to coating
- Easy to clean media debris and residue from critical areas, lubricity and release
- Results in reduced product defects, reduced downtime, scrap, and labor hours, increased production due to increase cycle times and reduced maintenance/setup and tear down, improved mold performance and reliability, higher margins on production runs, faster break even on mold manufacturing costs
Through precise, engineered deposits, Armoloy TDC®, XADC®, and Nyflon 25® add incredible value to plastic injection molding applications, as well as those in the areas of extrusion and thermoforming.
Particularly in the case of glass-filled resins, the Armoloy coatings improve cycle time and wear life by imparting a harder, more lubricious surface to molding components. Unlike many other surface treatments, the Armoloy coatings can be removed and reapplied, as wear life and maintenance schedules dictate, with no damage incurred by the base metal. Textured surfaces will retain their integrity after the Armoloy coating process. Considered a cold process, the Armoloy system prevents distortion, annealing, and dimensional changes from occurring in the base metal.
Increased material flow, reduced maintenance time, cleaner molds, and release of the formed part from the molding tool are additional advantages the Armoloy coatings offer to the plastics forming industry. In a current application for a high end office furniture manufacturer, The XADC® coating was applied for improved wear resistance, flow rate, and release. Time between maintenance cycles of the mold, which included expensive tear down and loss of production, increased from, on average, 12,000 shots to over 100,000 shots.
In addition to standard molding steels such as A-2, S-7, and H-13, the Armoloy coatings can also be applied to stainless steel, copper, beryllium, and bronze alloys such as Ampcoloy.
Common applications include core and cavity blocks, lifters, sleeves, ejector pins, bushings, rotating cores, and inserts.

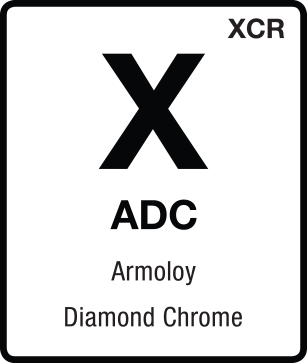

ISO 9001-2015 CERTIFIED